Achieving performance and excellence through 5S

As companies continuously strive to perform faster, better and at lower costs, operational performance is one of the main aspects they should look at. Since costs are also influenced by the quantity of waste or number of defects, organizations try to improve their performance by implementing Six Sigma, Lean, or Total Productive Maintenance initiatives.
Total productive Maintenance (TPM) represents a productive maintenance process that depends on the participation of all employees, so that the maximum equipment efficiency can be achieved within an organization. Therefore, in order to implement the Total productive Maintenance (TPM) at the operational level, Danaher and Toyota have shown that one solution is the implementation of 5S, as a methodology which fosters a culture of employee engagement. This a valuable technique for increasing performance through workplace organization capability & visual management standards. Moreover, 5S methodology allows the enhancement of efficiency and productivity, while providing a good working climate.
Hence, 5S represents a workplace organization plan defined by five Japanese key words: seiri, seiton, seiso, seiketsu, and shitsuke. If we translate these words into English, they all start with the letter “S”. Therefore, the 5 key words become: “sort”, “straighten”, “shine”, “standardize”, and “sustain”.
These steps used in the 5S technique are explained below:
- Sort: this action refers to sorting out the things that are needed and not needed in the working area. The idea is that work can become easier if obstacles are eliminated and if redundant items are removed and disposed in a red-tagged area. The sorting action requires the capabilities of a skilled supervisor, who will perform regular checks.
- Straighten: this action refers to arranging items in such a way that makes them easier to be used. Therefore, clear locations for the items should be determined so that they can be easily used. This step ensures an easier workflow and avoids loss and time waste.
- Shine: this action refers to constantly cleaning the workplace and equipment used, so that all standards can be maintained and defects can be diagnosed. In order to achieve this, it is recommended to keep the workplace clean and safe, and also invest in equipment maintenance.
- Standardize: this action refers to having a permanent overview upon the first three procedures and maintaining high standards throughout the workplace. Moreover, every best practice should be standardized and all the items should be kept in order.
- Sustain: this action suggests a continuous search for improvement and keeping in mind all the aforementioned steps. Moreover, regular audits should be performed and training activities should be given consideration.
The steps presented above show how a workspace should be organized in order to achieve effectiveness and efficiency, by looking at the items that should be used in the daily work, storing them properly, providing good maintenance both to the tools and the general work environment, and sustaining this newfound order. Another interesting approach to maintaining a high degree of performance and efficacy is ZARA’s, which looks at the same aspects previously mentioned, but from another point of view.
The standardization has to be discussed and agreed upon, so that a sense of understanding and engagement can be constructed in a proper manner, between all parties from top to bottom.
Therefore, this model fosters waste elimination, seeks to ensure a safe working environment through a permanent monitoring of all its items and through using data visualization for increasing the overall effectiveness. Moreover, the 5S scheme also follows the principle of cubic space within the organization and therefore, it is considered to be a simple and efficient 5-step model for continuous improvement within companies.
Image source:
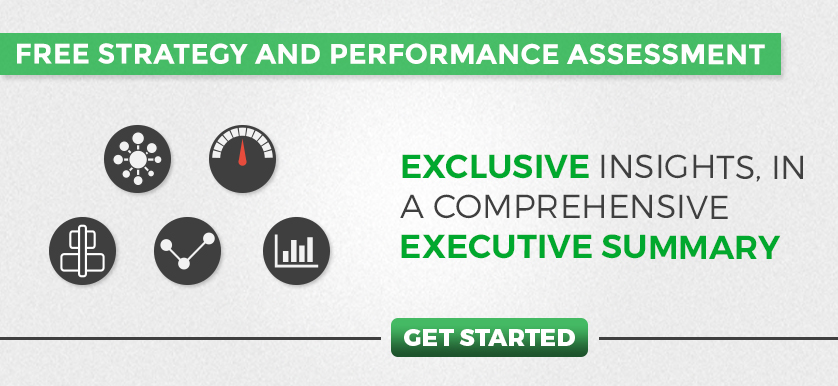
Tags: Employee Engagement, operational performance, Performance Culture