Is the Just-In-Time manufacturing strategy a sovereign, or a misleading system?
“Continuous improvement is not about the things you do well — that’s work. Continuous improvement is about removing the things that get in the way of your work. The headaches, the things that slow you down, that’s what continuous improvement is all about” – Bruce Hamilton.
For many ages, organizations desired to match supply and production with the anticipated demand in a way that would eliminate the stocking inventory. Most managers demanded high productivity levels in the assembly line, and counted on the Sales & Marketing Departments to sell those goods and create more demand. This continuous cycle led to a significant grow in inventories of unneeded products and also to difficulties in matching changing customers’ demands.
A system developed by the Japanese auto industry, the Just-in-time (JIT) manufacturing system, promised to eliminate waste and increase production quality for manufacturers, and also to eliminate backroom inventories for retailers. The Just-in-time manufacturing system is a production strategy aiming to increase processes efficiency by discarding excess inventory that is not valuable for the customers. In order to avoid costly storage and inventory management, this strategy underlines the fact that organizations produce what is necessary, when is necessary.
Just-in-time manufacturing system advantages:
- Waste reduction (transportation waste, waiting time waste, overproduction waste, inventory waste, processing waste);
- Efficiency increase;
- Inventory minimization;
- Quality focusing workforce;
- Strategy and forecasting accuracy;
- Easily shift to new customers demands.
Just-in-time manufacturing system disadvantages:
- Fluctuating transport size and cost;
- Uneven product procurement and disposal;
- Price and quality volatility (due to uneven purchases);
- Possible delays of final products or component transportation (road blocks, storms, and other unpredictable obstacles);
- Designing a new strategy for the entire work flow of the company;
- High initial investment for implementation.
Market experience underlines that having an inventory buffer (supplies that are kept at hand) will ensure no disruptions and smooth operations against the whole supply chain. However, an effectively planned just-in-time manufacturing system can develop higher-quality products by eliminating waste and increasing efficiency. Workforce must cope with the fact that nothing goes to waste, and that they are controlling and creating the value output. Everyone involved in the process relies on one important mission that is to be achieved: customer acquisition and retention, due to the high level of customization offered.
Just-in-time manufacturing system represents a good opportunity to introduce quality management or continuous improvement inside the organization, but it must be completed by other processes. Purchasing managers may need to implement other shipping models like less-than-truckload (LTL) which aims to efficiently fill a trailer transport with goods from different companies on a consolidated route. The workforce may benefit from just-in-time system by developing other skills and taking different tasks within the production process.
“We have found in buying materials that it is not worthwhile to buy for other than immediate needs. We buy only enough to fit into the plan of production, taking into consideration the state of transportation at the time. If transportation were perfect and an even flow of materials could be assured, it would not be necessary to carry any stock whatsoever. The carloads of raw materials would arrive on schedule and in the planned order and amounts, and go from the railway cars into production. That would save a great deal of money, for it would give a very rapid turnover and thus decrease the amount of money tied up in materials” (excerpt from Henry Ford, My Life and Work, 1923).
Jack Wilson wrote about successful implementations of just-in-time manufacturing system inside international well-known organizations.
Toyota Motor Corporation’s production strategy includes the procedure that raw materials are not released in the production cycle until an order is received and the product is ready to be assembled. No components are allowed at the production node unless they need to take part in the assembly of the next node. This procedure allowed Toyota Motor Company to have lower costs as a result of low inventory and a high degree of changing production to match customer’s tastes.
Dell, Inc. has a unique interpretation of the just-in-time strategy by providing short delivery times to their customers. This is done by “convincing” suppliers to manage inventory for them and deliver demanded components shortly, to help Dell Inc. simply assemble and deliver it to the customer. Harley Davidson Motor Company managed to decrease inventory levels by 75% and increase productivity after the implementation of just-in-time manufacturing system.
A successful just-in-time manufacturing strategy can provide significant benefits to the whole organization, starting with management and cascading to production cycle and employees. Therefore, the just-in-time strategy can bring the following benefits:
- Reduce scrap and rework rates;
- Reduce manufacturing lead times;
- Improve customer service level;
- Improve employee morale.
In order to remain competitive on the market, organizations are constantly looking at ways to adapt to customers changing tastes, sustainability and competitor challenges. Depending on different aspects like: industry, production level, selling market, the just-in-time manufacturing system can prove to be the life belt, or the growth method for an organization.
Image source: Pixabay
Image source: Pixabay
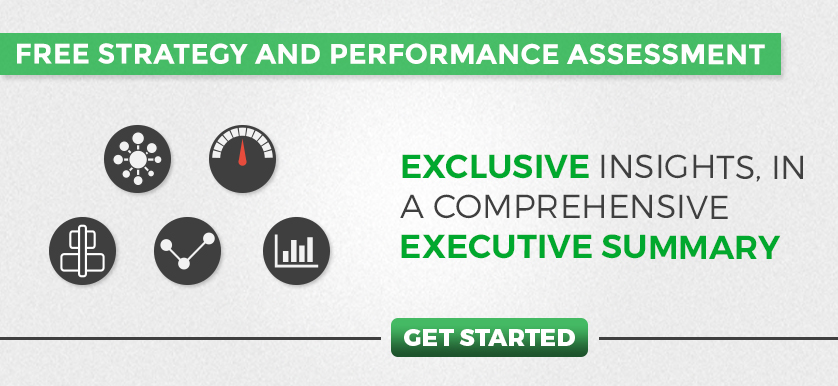
Tags: operational performance, Product Development, Strategy