Procurement performance at Siemens Wind Power A/S
By definition, procurement represents the process of obtaining goods and services from preparation and processing of a requisition to the approval of the invoice for payment. As Robert Monczka specifies in the book Purchasing and Supply Chain Management, purchasing is responsible for acquiring all the materials needed by an organization, and it is the function responsible for issuing purchase orders and initiating the flow of materials.
The terms “Procurement” and “Purchasing” are very often used interchangeably. It is argued that purchasing describes the actual buying, while procurement has a broader meaning, which includes different types of acquisition (leasing, rental, contracting etc.), as well as the associated work of identifying and selecting suppliers, negotiating, agreeing upon terms, expediting, monitoring supplier performance, analyzing orders, material administration and so on. However, these differences are mainly semantic and thus the focus is on the principle rather than drawing artificial boundaries around functions.
The procurement department’s mission at Siemens, the largest engineering company in Europe, is to provide the organization with the right amount of the right product, at the right time at world class costs. Procurement is divided into two departments within Siemens, the Strategic Procurement or Commodity Management department and the Procurement or Supply Management department. The split of responsibilities is clearly delimited.
The purchasing process
The Siemens overall supply chain includes planning, sourcing, making and delivering:
- The Sales department creates a load plan of turbines that need to be delivered to the customer;
- The Strategic procurement determinates the source of the materials, the suppliers;
- The Engineering department is responsible for creating the Bill of Materials (BOM) and thus the order for materials is created.
The application used by Siemens Wind Power, which centralizes the management of all resources is SAP (Systems Applications and Products). The program handles everything from people-oriented tasks such as payroll, sales, customer relations, and human resources to material-oriented tasks such as management of warehouses, supply chains and product life cycles. The materials requirement planning (MRP) of SAP has as a main objective to guarantee material availability. MRP is required to procure or produce the required quantities on time for internal purposes.
The load plan triggers the movement of materials through the company’s supply chain and initiates the flow of materials. This is given by a purchasing order (PO), which is essentially a message that Siemens send to a supplier, saying “We have agreed terms, so send us the following materials”. In reply, the supplier confirms the order and delivers the materials requested. Upon arrival, the delivery is controlled and the supplier is paid the agreed amount.
Communications with the procurement department
Procurement is in close contact with a number of other departments (as illustrated in the figure below). These linkages become even stronger and more important as purchasing continues to develop.
Internal integration means that purchasing develops its internal links with other departments. To successfully develop these links, the Procurement staff must have at least a working knowledge of the work done in different departments and, implicitly, other departments should know what procurement does. To improve internal integration, Procurement has to develop links with the following functions:
- Operational: Purchasing plays a leading role in supporting operations in making Siemens turbines. A major link between operations and purchasing is through their strategies, which are closely aligned and jointly developed. These links are also maintained at a tactical level. For instance, the operations load plan shows production levels over the next fiscal year, and this specifies the materials needed and their arrival schedule to be organized by procurement;
- Quality: The quality of materials brought into the company depends directly on procurement, so there is a clear link between the purchasing and quality management functions. Siemens puts very high emphasis on product quality and the materials need to respect the company’s high standards;
- Engineering: The design or new products, or changes to existing ones, is a central function of the Engineering department. For every material change, the Engineering department creates an ECN and the supply manager is informed about the change. Specific links between the two departments also occur when Engineering wants purchasing to identify the most technically capable supplier for a material, or to make sure that a supplier meets design’s specification. Also, Engineering and Procurement can form a stronger link when, for example, the two departments work together on product development or supplier selection, or Procurement can co-locate a buyer with Engineering to talk directly about the product and design and to respond quickly to their ideas.
- Accounting and finance: Despite the fact that procurement is responsible for acquiring the materials, it is accounting and finance that set budgets and administer payments. Within Siemens, this is organized electronically through electronic data interchange (EDI). For example, Procurement transmits a material release to a supplier, with details automatically passed to Accounting;
- Marketing and Sales: Procurement is concerned with moving materials into the company, while marketing and sales are more focused with moving turbines out to customers. But they are still connected as marketing develops sales forecasts that convert into load plans and material requirements;
- Legal: When purchasing signs a supply contract or PO, it makes a legal agreement with the supplier. The details of such an agreements are written by Siemens’ lawyers, and this needs close cooperation between the two departments. Standard terms are used for the contracts, so most time is spent on exceptional items or resolving disputes when things go wrong.
The Procurement department is in close contact with each of the above mentioned departments, especially when an issue arises and it needs to be solved. As for every company out there, it is suggested to organize a series of interdepartmental meetings where the staff of each of the involved departments can express its concerns and repeating issues, leading to a better cooperation and a better performance.
References:
- Siemens AG (n.d.) Supply Chain Management
- Business dictionary (n.d.) Procurement
- Purchasing Insight Ltd (n.d.), Definition of Procurement – Procurement vs Purchasing
- TechTarget (n.d.) SAP definition
- Abhijeet Guha (2010) SAP MRP Materials requirement planning
Image Sources:
- Monczka, R., Handfield, R., Hiunipero, L. and Patterson, J. (2010), Purchasing and Supply Chain Management
- Pixabay
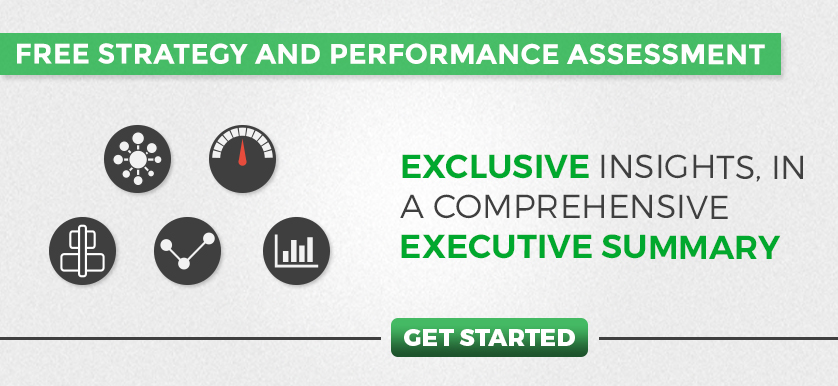
Tags: operational performance, Procurement performance, Supply Chain Performance