Toyota Motor Corporation and TPS – champions of performance improvement
Today more than ever, Toyota continues to be studied by scholars and professionals that are interested to understand how a handful of people that formed the early Toyoda family succeeded in setting one of the one world’s greatest manufacturers. It took decades of hard work, innovation and a unique philosophy to turn what was first a small manufacturer of looms used in the textile industry into a champion in the more competitive and tough automotive global market.
Why is Toyota interesting to study and understand? Because the Toyota Production System (TPS) is an example of great performance and innovation, of tools, philosophy and practices that not only outstand by their beauty, but have also proved their effectiveness, in the volumes of vehicles Toyota sold and continues to sell, its market capitalization, customer attitudes and preference for Toyota cars and, not less important, its overall corporate philosophy that has crystallized.
So what is the Toyota Production System and how it has made the company perform that well?
The TPS was developed by Toyota at the end of the World War II, when the automotive manufacturing industry was dominated by Ford and General Motors, which made use of big equipment, mass production and economies of scale to produce as much as possible with costs as low as possible (Liker 2004). What these two giants were lacking was a customer-oriented approach, clients desiring more flexibility and customization. So this was what Toyota needed to tackle, but how could it do it with not too high costs? The result was an innovative approach to the production process, with the major focus on eliminating waste from all stages beginning with the raw material and ending with the final product. And this stands at the base of the lean manufacturing concept that would be embraced by many other manufacturers in the world, with more or less success.
Several specific techniques and concepts were put in place, focusing on different areas of improvement, such as (Liker 2004):
- Just-in-time – the focus was to reduce inventories and associated carrying costs by using signals between different points in the process, which tell production when to make the next part;
- One-piece-flow – involved moving one workpiece at a time between operations within a workcell;
- Jidoka (‘automation with human intelligence’) – meant freeing the equipment from the necessity of constant human attention, separate people from machines and allow staff to conduct multiple operations;
- Kaizen – described the focus on small, incremental, continual and adding-value improvements;
In this context, several KPIs can be used to measure performance in the production process (Liker 2004):
- # Lead-time to produce
- # Work-in-process inventory
- # Finished-goods inventory
- # Overtime
- # Productivity (pieces per man hour)
However, for long-term success and sustainability of the operational excellence, techniques must be supported by an organizational philosophy that frames the context of operations. And Toyota understood this, establishing several immutable principles (Liker 2004) that would guide its existence over decades:
- Long-term thinking, focus on adding value to the society
- Performing the right processes leads to the right and desired results
- Develop Toyota’s people and partners
- Solve root problems, thus drive organizational learning
Reference
- Liker, JK 2004, The Toyota Way: 14 Management Principles from the World’s Greatest Manufacturer, McGraw-Hill
Image Source
- toyoland.com (2010)
Note
For more KPI examples in Production and Manufacturing, visit smartKPIs.com.
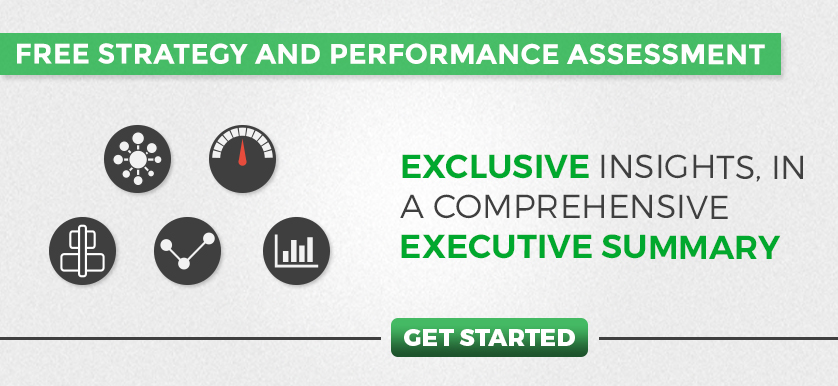
Tags: Improvement, Manufacturing performance, Performance in Japan, Performance Management, Toyota