Benchmarking for total quality management
In Juran’s opinion, organizations need to ask themselves what their competitors do in order to perform at a high level. To find out the difference between performance results, companies introduce benchmarking as an approach for organizations that have adopted total quality management (TQM).
Benchmarking is acknowledged, nowadays, as being a core component of the quality improvement methodology and it can be regarded as the most important contribution to it after Deming’s or Juran’s foundations. Benchmarking has the main purpose of assessing an organization’s strategy, products, and processes, and comparing them with those of the world’s best-in-class organizations. Benchmarking can bring several benefits to the organization, including cultural change, improved performance and better trained employees.
However, the term was clearly defined in the 1980s, when the Xerox benchmarking program was initiated by Robert Camp. The benchmarking idea could have started in early 1950s, when Deming introduced the idea of quality control and the 14 Points on Quality Management as a basis for implementing the total quality management system. It is intended for helping organizations increase their productivity and process quality. At the same time, Juran‘s contributions to quality management might have been even greater, as he focused on the responsibility of management to achieve quality and the needs for setting goals.
Toyota production system (TPS), which represents Toyota’s management system, is one of the most benchmarked business improvement strategies used in the modern industry. Of course many companies try to replicate Toyota’s success by using various techniques, but practitioners face difficulties when figuring out the ways in which Toyota replicates its production system with suppliers and transfers its in-house best practices.
In achieving high performance, Toyota targets processes pertaining to offering suppliers assistance to have a more effective management.
Moreover, Toyota represents an example of management innovation in quality control, having introduced the Just-in-Time system, which represents an adapted version of Ford’s Just-in-case System.
Just-in-Time production is a high performant technique which refers to meeting the challenges and fulfilling the demands through efficient and cost-effective ways. Just-in-Time promotes an optimized workflow, with planned cycle times, that significantly reduces costs through an optimum supply-chain and “zero stocks”. According to the existing literature, Taiichi Ohno adopted the first JIT manufacturing method at a Japanese car plant in the 1970s.
Just-in-Time, as a key to performance, redefined the manufacturing process and cut unnecessary costs by supplying parts only when the process required them. This approach eliminated the need to have buffer stocks and encouraged employees to be more involved in logistics and inventory aspects related to their daily needs. Moreover, Just-in-Time offers the possibility to have a simultaneous production process for different product models, compared to a traditional production process where manufacturing is based on producing a single model at a time.
According to The Economist, there are a lot of aspects to be taken into consideration when implementing a Just-in-Time system. The most important ones refer to “steady production, flexible resources, extremely high quality, no machine breakdowns, reliable suppliers, quick machine set-ups, and lots of discipline to maintain the other elements.”, as stated in the article published in the Economist.
The best description of the JIT concept was provided by Henry Ford in his 1923 book, My Life and Work, where he states:
“We have found in buying materials that it is not worthwhile to buy for other than immediate needs. We buy only enough to fit into the plan of production, taking into consideration the state of transportation at the time. If transportation were perfect and an even flow of materials could be assured, it would not be necessary to carry any stock whatsoever. The carloads of raw materials would arrive on schedule and in the planned order and amounts, and go from the railway cars into production. That would save a great deal of money, for it would give a very rapid turnover and thus decrease the amount of money tied up in materials.”
Mainly, the Just-in-Time model is used to eliminate the types of manufacturing wastes. Combined with benchmarking, companies can ensure a total quality management system and also compare themselves with best-practice companies in the industry.
References
- Marksberry, P. (2012) Investigating “The Way” for Toyota suppliers: A quantitative outlook on Toyota’s replicating efforts for supplier development, Benchmarking: An International Journal, Emerald Insight
- The Economist (2009), Just in time
- Toyota (2014), About us, Toyota Production System, Just in time
Image Source
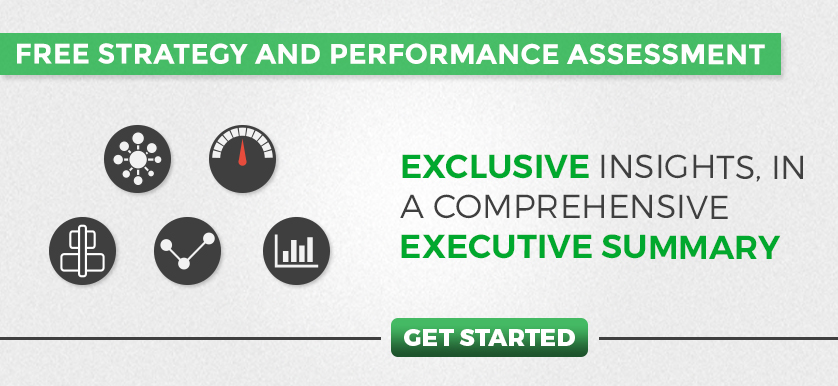
Tags: Automotive performance, Performance Management, Total Quality Management, Toyota Production System