The 5 S’s that bring you closer to performance
Achieving predefined targets within the organization frequently relies on indirect influential factors which can act as an enhancing element or as an impediment in the performance management process. One such factor is represented by having an organized workplace, which is based on five main principles that are to be implemented and further followed.
Among the powerful Lean Manufacturing Tools there is the 5S workplace organization method, a highly effective tool, if successfully implemented.
The method implies adhering to a list of 5 tasks, originally expressed in Japanese as: “seiri, seiton, seiso, seiketsu, and shitsuk” which translates into the following: “sort”, “straighten”, “shine”, “standardize”, and “sustain”, ergo, you have the 5 S.
This represents a simple method for employees to organize their workplace in a clean, efficient and safe manner that will enhance and enable their productivity and, implicitly, their performance. Additionally, it enhances visual management, in order to ensure an introduction to a standardized and highly performing work place. The main purpose when implementing 5S is the organization’s need to introduce standardized and operational practices which guarantee efficient, repeatable, safe ways to work within the company.
A standardized work flow provides the company with a solid foundation for building all of the other improvements that come with implementing Lean Tools. Also, it simultaneously provides a highly visual workplace. Performance is reached through one of the most important aspects of the 5S method, which is the fact that it highlights problems and makes them immediately obvious.
5S is a process that relies on the team’s self-management ability. This means it that needs to be conducted by the employees who work within the designated space in which the 5S principles are being implemented and cannot be applied by an external collaborator without the comprehension and cooperation of the employees activating there.
Process wise, the 5S follows these steps:
- The implementation of a 5 S project starts with taking action, more specifically defined as the “Sort” step. It begins with addressing the matter and taking action for what is actually necessary to employees in order to perform their daily work. An office can be compared to an expensive real estate: only those items which add value to the daily work are worth keeping on employees’ desks. In cases of doubt and incertitude it is recommended for the items to be moved out, or even better, in order to encourage an environmentally conscious spirit of recycling among employees, the items can be given or exchanged with someone who needs them. A sorting initiative within the workplace, for example through drawers, will free up a large space. It is recommended to firstly review the company’s retention policy before initiating this kind process, as such a step helps in making faster decisions and provides permission to either hang on to an item or discard it. The Sort process, can be speeded up by having a large trash can available, as well as a shredding bin.
- “Straightening” up the working area or setting it in order is the second step within this process, through which employees seek to create specific locations for files, objects and equipment. This step helps organizing things used more often, by assigning a designated, specific location for them. Setting in order is often done using duct tape to create an outline on your desk for each item or desk accessory. Through this approach, employees are instantly able to see if something is missing or out of order. Labels also represent a helpful kit in the straightening stage, as they can be applied to individual shelves, cabinets, and drawers within the office. They will serve as a visual reminder for the employees of what goes where and will help in keeping them from stashing materials where they do not belong.
- Moving to 5S’s third step: “Shine” or “Sweep”, all surfaces and spaces can be easily accessed and used. For the technical equipment, the IT or other specialists can be approached in order to get hints about best recommendations on how, and with what, to clean equipment. The step ensures a long lasting life and better functionality of the equipment in use.
- The fourth step refers to bringing “Standardization” into the work place, due to the fact that it allows for systems to be placed in such a manner that every employee will follow the same procedures, in the same way. It implies creating an applied form for inbound calls, a color-coded filing system or using a checklist before sending products outside the company. Standardized processes and procedures decreases the error rate, more specifically the waste of defects and ensures that 5S techniques are being applied. Developing standardized forms for inquiries, in electronic or paper format, ensures that standard information will consistently appear in the same format.
- After developing a daily working routine from “Sort”, to “Straighten”, “Sweep” and “Standardize”, the final step of 5S is represented by the “Sustain” action. It is recommended to develop a checklist to serve as a reminder in order to sustain all of the new effective work flows.
Recently, a sixth S has come to attention and concerns “Safety”, which has to be put first and considered when implementing any other of the previous steps.
References:
- Thomas, A. (2014), 5S in the office today
- Lean Manufacturing Tools (2012), What is 5S; Seiri, Seiton, Seiso, Seiketsu, Shitsuke
- Lean Manufacturing Tools (n.d.), 5S office; implement the lean office
Image source:
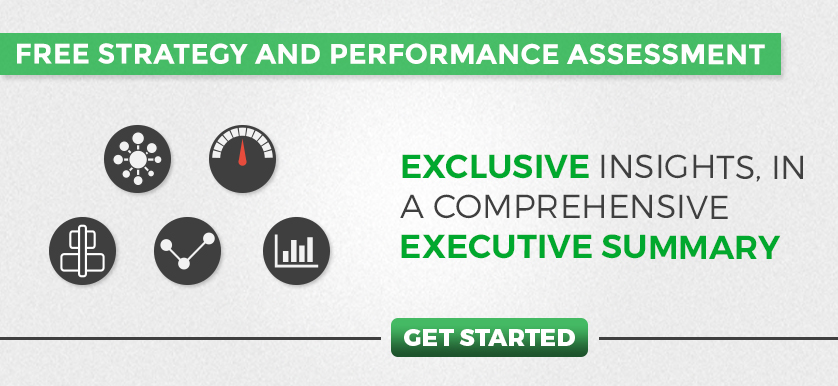
Tags: Employee Performance, Lean Manufacturing