The implications of Modern Quality Management in benchmarking

A prerequisite for a successul benchmarking study is to have a Total Quality Management system in place within the organization. Modern quality management entails customer satisfaction, it prefers prevention against inspection and it recognizes the managerial team’s responsibility for quality.
Several remarkable persons in the management field, like W.Edwards Deming, Joseph M. Juran, Philip B. Crosby, Koaru Ishikawa Genichi Taguchi and Arnold V. Feigenbaum, brought excellent contributions to the development of modern quality management.
Besides Deming, Joseph Juran settled the basics of benchmarking with his contribution to modern quality management. Joseph M. Juran has brought significant input in regards to productivity issues. In 1984, he wrote the first edition of the “Quality Control Handbook,” which stresses the importance, for management, to be engaged in the continuous development of products.
He developed 10 steps for quality improvement:
- Assess needs and improvement opportunities;
- Set goals for improvement;
- Become an organization focused on achieving goals (establishment of a Quality Council, identification of problems, selection of projects, establishment of teams, facilitators);
- Facilitate trainings;
- Initiate projects to solve issues;
- Report progress;
- Recognize merits;
- Communicate results;
- Track scores;
- Focus on annual improvements so that they become usual processes within the organization.
Quality planning
Regarding quality, it is very important to develop a plan to ensure the quality of the project, but also to be certain that the products or services delivered respect, indeed, high quality standards. Hence, delivering high quality implies all the activities needed to achieve the important quality standards that had been demanded.
Some instruments used in quality planning can also be used in quality insurance. Experimental projection can be helpful in ensuring a high quality product. Comparison standards, or the benchmarks used, can be adopted to generate ideas in regards to quality improvement by comparing project specific practices, or product characteristics, to the ones belonging to other projects, or products, within or outside the organization that produces them.
One of the main instruments and techniques in quality insurance is the quality audit. Quality audits represent structured reviews of specific activities of quality management, that help in identifying best practices which can improve current and future projects. Quality audits can be scheduled or not and they can be conducted by internal auditors or by third parties with relevant experience. For example, engineers can conduct quality audits by helping to project specific measure units for a project’s quality level, then applying and analyzing these measures by using the project.
Quality control
It is very important to distinguish between quality control, planning and quality insurance.
Even if one of the main goals of quality control is still the same, to improve quality, the main outputs of this process are the acceptance decisions, reviews and adjustments of process.
- Acceptance decisions: decide if the products or services executed as part of the project will be accepted or rejected. If the project’s stakeholders reject some of the products or services that are part of the project, these have to be reworked.
- The rework: it refers to the action designed to align the project, or service, to the exact specifications or to the stakeholders’ expectations.
- Process adjustments: correct or prevent future quality problems based on quality control measurements.
Quality control instruments
There are a lot of instruments and techniques that can be used in quality control. However, some of the main techniques refer to: the Pareto analysis, statistical sampling and quality control diagrams.
- Pareto analysis: implies the identification of the main factors that cause the most quality problems in the system. Sometimes, it can be linked to 80-20 rule which means that 80% of the problems are a result of 20% of the causes.
- Statistical sampling: it’s a key concept which refers directly to project management quality. Statistics and especially concepts like statistical sampling, safety factors, variation and standard deviation are fundamental concepts for understanding diagrams in quality control.
- Quality control diagrams: refer to diagrams that illustrates the results of a process in time and help in preventing defects.
In order to ensure high standards, top managers should use all these techniques for modern quality management and make sure that they have the quality system implemented prior to starting a benchmarking implementation process within their organization.
References- The Juran Institute (2014)
- Juran, J. (2010) Juran’s Quality Handbook: The Complete Guide to Performance Excellence, Sixth Edition
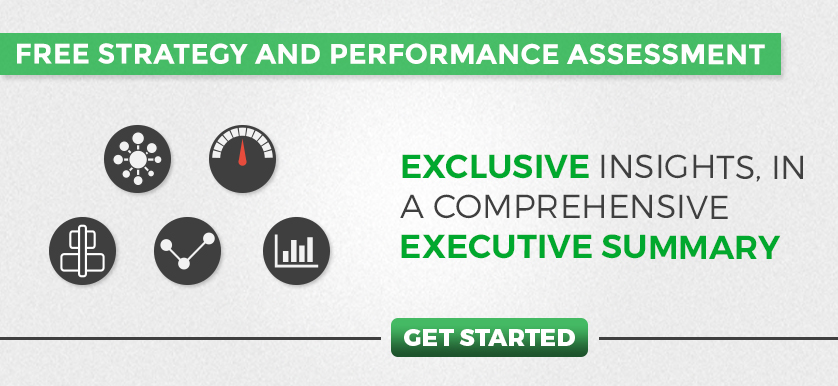
Tags: Benchmarking, Production and Quality Management performance, Quality Improvement